Next up… Seat Rib Subassembly! (In reality I was intertwining center section sessions with seat rib sessions because of the spacer delays, but this post represents all the hours spent on the seat rib subassembly so far). I got a lot of help from a ton of folks for this work. Trusty Sam and Tod, but also Nico and Sam’s younger kid Ryden helped out! If it’s not clear what the seat rib subassembly is, it’s the floor assembly where the seats will be installed just aft of the center section. See the drawing detail below:
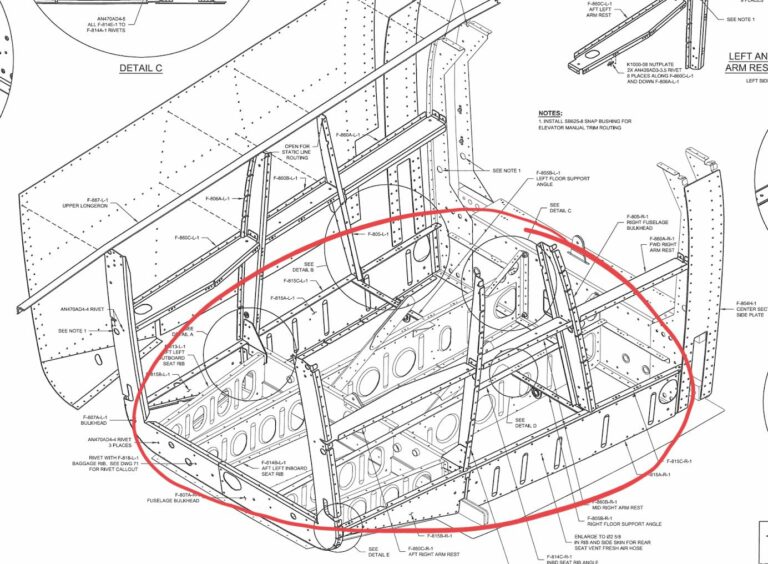
5/2-5/6 - Warriors and Seat Rib assembly
As usual, we start with finding all the parts, de-vinyling (yes…I just made up that word) them, labeling, and clecoing stuff together. I focused on the rear spar attach assembly, while Sam and Tod fabricated some of the more complicated parts from aluminum bar and angle. All while stressing about Warriors Game 1. It was an ugly loss, but a fun working session. The F-805D seat brackets were a bit complicated, so took a couple tries to get right, but Sam worked his way through it. On the rear spar attach assembly, the only complicated part was match drilling the #12 hole through the two attach bars. You needed to set up the drill press configuration just right to cleanly get through both bars and maintain the space between them. See the pictures below for how I ended up setting it up.
5/6 - Saturday solo session
In the next session, I spent most of my time doing full assembly of the subassembly to ensure fit. Since I’m doing electric aileron trim, I had to do some extra work for that kit. There are a few brackets that need to be attached to the spars. The instructions imply there is a lot of cutting out of holes in the spars to make this work, but after closer inspection it looks like those holes are already pre-drilled now. There are even pre-drilled holes for easier match drilling through the spar. I didn’t figure that out until I was measuring for the hole cuts, and realized that the holes were already there! Another challenge was the match drilling of the seat brackets (F-805D). You are required to level it against the top of the rib, and it’s quite hard to clamp it down for drilling. One I got pretty well, but the other is not quite perfect. I think it’ll do but I may need to make some adjustments later.
After I dealt with the electric trim kit bracket I continued with assembly. It was fun seeing the skeleton come together. At various stages I final size drilled connecting holes. Once the skeleton was fully assembled it was time to flip it upside down on some saw horses to fit the bottom skins. Normally I would then need to final drill and deburr those holes but since I have the special dimpling dies from Synergy, I got to skip that step. One interesting note (and noted in the instructions) was that one of the skins doesn’t match the curve of the ribs, and because there is a stengthening flange, it won’t naturally bend to fit the curve. So fluting is required to match the curve.With the test fit going well I pulled off the skins and rolled the edges as instructed. The session was quite a long one so it was time to head home for the day!
5/7 - Sunday Funday! (and priming)
With the skeleton test fitting complete it was time to uncleco everything, deburr rivet and lightening holes, clean up the edges, then clean, etch and prime the parts. A crew came out to help, and through the long day we got everything primed and drying for final assembly! Thanks to all the hands (and the semi-permanent priming setup), we were able to get a fairly sizeable set of parts primed in a reasonable amount of time.
It was a fun day of work, and play. We took some breaks to have a yummy Bahn Mi lunch, and a bit of goofing off racing other RC toys around the airport (see below). All in all, a great weekend (and week) of building. Next up will be final assembly of the seat rib subassembly. Until then… Happy Building!
1 comment
Good work as usual. Love the human and modem 3 racing with toy car at the end. It is good to have double doses of fun